La impresión 3D, disrupción en su momento convertida en realidad, ha llegado a cotas inimaginables hace tan sólo unos años, con hitos como el lanzamiento, en marzo de 2023, del Terran 1 de Relativity Space, el primer cohete impreso en 3D (hasta un 85%). Puesta de largo que se verá ratificada con el lanzamiento del Terran R (2026), con el desafío de superar los requerimientos ‘Max Q’, el estado de tensión más exigente en estructuras impresas.A diferentes niveles atmosféricos, la impresión 3D (la fabricación aditiva) demuestra la efectividad de su creación de piezas (miles de ellas) y estructuras capa a capa, sobre todo en el metal, con un significativo incremento de eficiencia en los últimos años (además de materiales como el termoplástico, que llega a suponer un 50% menos de tiempo de producción). Con piezas más ligeras y sostenibles, que cuesta menos y se fabrican más rápidamente, sometidas a los más elevados estándares de seguridad, con la IA también presente en este tipo de procesos (en tiempos en los que contribuye a desarrollar -y hasta crear- nuevos materiales, como sucede en el caso de la NASA, que ha patentado una nueva aleación idónea para la impresión 3D de inyectores de combustible). La doctora María de Nicolás, ingeniera aeroespacial e investigadora postdoctoral del Instituto IMDEA Materiales, doctorada en Ciencia e Ingeniería de Materiales de la Universidad Carlos III de Madrid, resume la esencia de este proceso: «Esta técnica de fabricación permite obtener geometrías complejas con una reducción en el desperdicio de material, contribuyendo al ahorro energético y reducción de la huella de carbono». Una baza para la sostenibilidad del siglo XXI «en la que su combinación con la optimización topológica de superficies es capaz de conseguir estructuras de menor masa con iguales o superiores prestaciones, puntos fundamentales en el ahorro de combustible».Noticia Relacionada estandar No La impresión 3D da un brillo de personalización al sector joyero Laura Montero Carretero Pequeños proyectos que buscan diferenciarse y grandes firmas exploran las posibilidades de esta tecnología en el diseño y la creación de piezasDe impresiónSobre el terreno, De Nicolás destaca las diversas investigaciones en el instituto en el entorno de impresión 3D de materiales para motores de aviones, «como en el caso de las aleaciones base Ti y Ni. Contamos con una estrecha colaboración con ITP Aero, con base en Bilbao, pionera en impresión 3D de estructuras de motor, como el TBH del motor UltraFan®, así como en el desarrollo del primer motor aeronáutico propulsado por hidrógeno, objetivo del proyecto Cripicom (primeras pruebas están previstas para 2025)». En este escenario global ( drones incluidos) confluyen las compañías fabricantes (como Boeing o Airbus) con las que fabrican motores, con ejemplos multisector como General Electric o Rolls Royce. En el caso aeroespacial, las agencias espaciales NASA (EE.UU.) y ESA (Europa) también desarrollan tecnología en este sentido, con ejemplos como el modelo de motor RDRE (motor de cohete de detonación giratoria), capaz de enviar una nave espacial de la Luna a Marte, o una impresora 3D de metal, diseñada por Airbus, pionera de fabricación europea a integrar en la Estación Espacial Internacional.Airbus también cuenta con colaboraciones como la de Trumpf, que le suministra impresoras 3D de metal para el desarrollo de modelos como el CityAirbus eléctrico, el helicóptero experimental de alta velocidad Racer y los Airbus A350 y A320. Una importante aportación, como también ha sucedido con otras colaboraciones como la propia de la empresa española Aernnova, que ha realizado prototipos de piezas en la fabricación aditiva (3D) en concreto para el Airbus 350, y para ensayos de Lilium («la fabricación aditiva (destacan desde la compañía) es una tecnología que está en nuestro radar y estamos siempre dispuestos a trabajar en ella de la mano de nuestros clientes».Campo abiertoReinforce3D, con sede en Tarragona, es otra de las valiosas aportaciones españolas. La compañía, ‘spin off’ de Eurecat (Centro Tecnológico de Cataluña), preparó, vía impresión 3D, el soporte de aluminio para la antena de un satélite, con el resultado de conseguir la resistencia necesaria con un 70% menos de peso. Innovación que ha supuesto uno de los premios 3D Pioneers Challenge de Rapid.Tech 3D, destacado punto de encuentro internacional del I+D+i en impresión 3D.Desde Pangea Aerospace, su CEO y cofundador, Adrià Argemí, destaca, por su parte, cómo «sin la impresión 3D metálica, no hubiéramos podido hacer nada de lo que hacemos para cohetes, satélites y otros vehículos espaciales. Nos da libertad de diseño, permitiendo crear formas muy complejas que no se pueden lograr con la fabricación tradicional, y esto es la clave de nuestras innovaciones».Piezas fabricadas por Hiperbaric Propuestas de muy altos vuelos Como única compañía española que fabrica equipos de HIP (Hot Isostatic Pressing), Hiperbaric inauguró en Burgos en 2021 el primer Centro de Innovación HIP que existe en el sur de Europa. La tecnología de prensado isostático en caliente consiste en aplicar 2.000 bares de presión y hasta 2.000°C de temperatura a las piezas metálicas o cerámicas, lo que elimina la porosidad de los componentes de alto rendimiento. Además de mejorar las propiedades mecánicas por Fabricación Aditiva Metálica (3D), el HIP aumenta la resistencia frente a la fatiga y da lugar a piezas con microestructura de grano fino con buenas propiedades mecánicas, entre cuyas aplicaciones destacan las propias del sector aeronáutico «muy garantista, que requiere materiales muy resistentes». Innovación sin cesar, como también sucede con Pangea, que actualmente trabaja en líneas de producto como sistemas de propulsión (por ejemplo, para satélites o vehículos de transferencia orbital) o los motores para cohetes de diversos tamaños.Sistemas de enfriamiento óptimos (motores más eficientes y de menor coste) o motores con tobera ‘aerospike’ (aumentan la eficiencia de un motor de cohete en un 15%, incrementando la rentabilidad hasta en un 50%) son dos de los desempeños que sitúan a esta empresa española «como pioneros en Europa en diseñar, fabricar (en sólo dos piezas) y probar un motor con tobera ‘aerospike’ en Europa. También somos los únicos en Europa (aparte de la NASA en EE.UU.) en probar cámaras de combustión impresas con dos materiales distintos en la misma máquina, lo que permite reducir el coste y el peso del motor drásticamente».Conductos de aire, horquillas, piezas del interior (consideradas ‘poco críticas’ para el vuelo), bordes de alas… todo suma en esta nueva concepción de la ingeniería aeroespacial, más allá del propio diseño de estructuras y motores. Como destacan María Jesús Casati, directora del Departamento de Aeronaves y Vehículos Espaciales de la Escuela Técnica Superior de Ingeniería Aeronáutica y del Espacio (Etsiae) y profesora titular de la UPM, y Daniel Barba, profesor contratado doctor en la misma institución (investigador en Fabricación Aditiva de Aleaciones Aeroespaciales): «La adaptabilidad entre el diseño y la fabricación final aportan un valor indispensable a esta metodología. Se dispone de una amplia gama de materiales que permiten el diseño preciso, e impresión a gran escala con producción de piezas más ligeras y versátiles».Una de las piezas realizadas en la compañía española Hiperbaric, con sede en BurgosVías abiertasEn este ‘estado del arte’ los especialistas de la Universidad Politécnica de Madrid subrayan la importancia de reducir peso «lo que supone un importante ahorro de combustible: se estima un descenso en las emisiones de dióxido de carbono, de un 1% aproximadamente por cada reducción de 500 kg (el peso de un avión comercial está entre 150 y 200 toneladas)». Sostenibilidad en marcha para varios grupos de la Etsiae, que trabajan, por ejemplo, en el prototipado de UAVs (vehículos aéreos no tripulados) «como el VTOL de despegue vertical, realizado con un filamento LW-PLA, polimérico fabricado con materiales renovables que utiliza tecnología de espuma activa para reducir peso y densidad».Estas técnicas crean geometrías complejas y permiten reducir el desperdicio de materialFilamentos como el poliéster de cetona de éter se unen a este conglomerado de desarrollos, en el que los investigadores destacan también «el uso de aleaciones aeroespaciales, que supone ahorros significativos de peso, coste de material y nuevas funcionalizaciones, imposibles de concebir mediante procesos de fabricación convencionales, con ejemplos como la aleación GRX-810 explícitamente desarrollada por la NASA para fabricación aditiva, pensada para su uso en los inyectores de combustible de motores supersónicos, y que se espera que reduzca la emisión de gases contaminantes y el peso del motor». Otro punto clave en la fabricación aditiva, en este ‘work in progress’, es el control de la ‘repetitividad’ de las propiedades de los componentes «para vigilar las variabilidades en sus propiedades mecánicas, una de las principales barreras para su adopción en la industria aeroespacial».
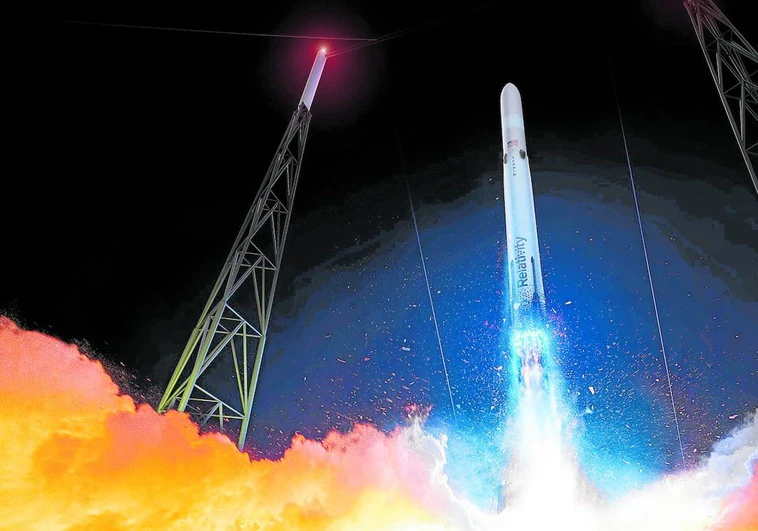
Leave a Reply